At the end of the HASTECS project: "a great success for the powertrain of future hybrid electric aircraft that are more respectful of the environment"
The July 13, 2021
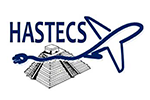
The HASTECS -Hybrid Aircraft project; Academic reSearch on Thermal and Electrical Components and Systems-, carried by the LAPLACE laboratory (Toulouse INP-CNRS-UPS) and part of the European program "Clean Sky 2" (H2020) exceeds the expected results. It identifies the most promising technologies and breakthroughs, innovative tools to increase the efficiency of electrical processes and reduces the embedded masses in hybrid propulsion systems for future aircraft that are more respectful of the environment.
Ambitious goals:
The HASTECS project (Hybrid Aircraft; Academic research on Thermal and Electrical Components and Systems), an integral part of the European program "Clean Sky 2" (H2020) took off in September 2016. It aimed to identify the most promising technologies and breakthroughs and to innovate in tools that make it possible to increase the efficiency of electrical processes and reduce the on-board masses in hybrid propulsion systems for future aircraft that are more respectful of the environment. These objectives applied to the case of a regional aircraft, sized for approximately 70 seats with a range of less than 1000 km. A series hybrid architecture was chosen by Airbus, coupling a gas turbine and an auxiliary power source with fuel cells or batteries to supply a 100% electric propulsion chain.
But these goals cannot be met if the specific powers are not high enough: the HASTECS consortium has thus set itself the challenge of doubling the specific power of electric machines with cooling and increasing it by 5kW/kg, for a technological target in 2025, at 10kW/kg in 2035, while the power electronics (cooling included) would evolve from 15kW/kg in 2025 to 25kW/kg in 2035, despite particularly severe environmental constraints (thermal, partial discharges, etc.). To give an idea, the motorization of a Tesla electric vehicle displays a specific power of less than 4kW/kg for the motor with its cooling ...
Leader of the HASTECS project, LAPLACE (UMR CNRS - Toulouse INP - UPS), for power conversion, has joined forces with the l’institut P’ (UPR CNRS located at ENSMA Poitiers) for the cooling of electrical machines and power electronics, Toulouse INP coordinating the project.
A real technological and scientific success
On Friday April 23, 2021, the last of the 6 doctoral theses was supported, with also two post-doctorates associated, thus bringing a very fine finish to a scientific adventure particularly rich in results and scientific exchanges.
It should be noted from the outset that all of the project's expectations have been fulfilled. In particular, the targets in terms of specific power (power - mass ratio) and energy efficiency were even exceeded, which "would contribute to the weight loss and efficiency of a future aircraft"!: HASTECS is therefore a real technological and scientific success, punctuated by an abundant scientific production, many publications with the teams and research institutes of the consortium, bringing successful interdisciplinary research.
6 doctoral students for 6 Work Packages: "very collaborative work for an integrated project"
High performance electric motors
The design of electric motors carried out by the GREM3 team of LAPLACE leads to high specific powers, exceeding 11kW/kg by integrating the cooling system, with high efficiencies, greater than 97%. This design has been obtained thanks to high performance permanent magnet synchronous motor with Halbach structure. The optimization under constraints of current densities, magnetic fields and the increase in rotation speeds are key drivers to which has been added the use of special windings (compact rectangular Litz wires) and high performance ultra-thin magnetic sheets to limit high frequency copper losses and iron losses: this is what makes it possible to obtain excellent efficiencies exceeding 97%. But optimising the electromechanical conversion is nothing without an equally powerful cooling system. This is the case of the concepts proposed by l’institut P’ which combine glycol water cooling for the stator and the rotor, to which it was necessary to couple an internal cooling, directly within stator slots, to achieve such specific powers.
Electric motor: left - high density magnet synchronous machine design levers; right: internal and external engine cooling
Optimisation of power electronics and high voltage network
In order to efficiently convert the power between the electric distribution (high voltage DC bus) and the electric motors, solutions have been proposed by the “Convertisseur Statique” team at LAPLACE to optimise the integration of power electronics. The joint use of a high voltage bus (close to 2kV), with its optimised mechanical structure (bus bar), the best electronic components (7th generation IGBTs) and modulation strategies also optimised for various multilevel conversion structures has proven to be particularly effective in terms of compactness and efficiency (yield of the order of 99%). As with the machine, optimising the power electronics is nothing without a very high performance cooling system. This is the case with the concepts studied by the l’institut P’ and the GREPHE team at LAPLACE, which proposed ultra-efficient two-phase capillary pumped cooling systems: the device is capable of extracting 4.5kW of heat losses for 1 kg of cooling system, allowing the complete power conversion system to greatly exceed 30kW/kg, well beyond the targets set!
Power electronics: left - multi-cellular structures; right: two-phase cooling by CPLIP (capillary pumped loop for integrated power)
Fuel cells 2 times more compact in specific energy than the best "energy batteries" by 2030.
A study carried out jointly by CIRIMAT and LAPLACE (GENESYS group) also concerned the auxiliary electrical sources hybridized with thermal sources (gas turbine): the conclusions show that, for this case of application to series hybrid regional aircraft, fuel cells with cryogenic hydrogen storage (stored at 20°K in liquid form) are almost twice as compact in specific energy (Wh/kg) than the best “energy batteries” by 2030.
Optimised system integration: an improved compromise between on-board weight and kerosene consumption
Finally, one of the major expectations of the HASTECS project was the definition of the voltage level of the electric distribution (HVDC bus) which constitutes a significant coupling factor on the mass of the main components (electrical machine, power electronics, wiring, etc.) by integrating environmental constraints specific to aeronautics. In this context, an in-depth study on the impact of partial discharges in the electrical machines insulators and power electronics was carried out by the MDCE team of LAPLACE. In the end, the best system compromise on the choice of this voltage is between 1300 and 2000V. This result could not be obtained without the overall optimisation of the propulsion chain carried out by the GENESYS team at LAPLACE: all the technological choices and scientific concepts were integrated through surrogate models making it possible to offer a global vision on the complete propulsion chain, from sources to propellers.
Optimal design of the complete hybrid electric propulsion chain
Ultimately, these optimized integration results lead to an improved compromise between on board mass and kerosene consumption compared to the targets initially set for the project.
The HASTECS project has received funding from the European Union’s Horizon 2020 (cleansky 2 JTI) research and innovation program (2014–2024), under grant agreement No. 715483.